Large Scale Cement Production in Nigeria; The Feasibility Report.
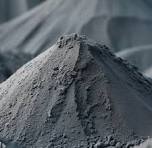
Nigeria’s rapidly expanding construction and infrastructure sectors have created an ever-growing demand for cement, positioning the country as a significant player in Africa’s construction market. With a population exceeding two hundred million (200,000,000) and increasing urbanization, the need for building materials is at an all-time high.
Establishing a cement plant capable of producing twelve thousand (12,000) metric tons per day presents a substantial investment opportunity that can address domestic needs while tapping into regional export markets.
This analysis evaluates the economic feasibility of such an investment, focusing on market dynamics, production processes, resource availability, costs, and challenges.
The cement market in Nigeria is driven by diverse factors. Population growth has intensified the housing deficit, estimated at 16 to 17 million units, creating sustained demand for cement. Large-scale government infrastructure projects, such as roads, bridges, and dams, further amplify this need.
Simultaneously, private sector investments in commercial and industrial projects also rely heavily on cement, underscoring its importance in Nigeria’s economy. While leading producers such as Dangote Cement, Lafarge Africa, and BUA Cement dominate the domestic market, some regions still face supply shortages, leading to price fluctuations and creating opportunities for new entrants.
Furthermore, Nigeria’s geographic location and proximity to other West African countries offer significant export potential, particularly in nations with limited cement production capacity.
Raw material availability is a critical consideration for cement production. Limestone, the primary raw material, is abundantly found in states such as Kogi, Ogun, Benue, and Edo. Other essential materials, including clay, gypsum, and pozzolanic materials, are also readily available locally, although some high-grade components may require importation. The availability of these resources provides Nigeria with a competitive edge, reducing raw material procurement costs for cement manufacturers.
The cement production process is capital-intensive and technologically sophisticated. The process begins with the extraction of limestone and other raw materials, which are then crushed and mixed in precise proportions to create a fine powder known as raw meal. This mixture is fed into rotary kilns, where it is heated to temperatures exceeding 1,450°C to form clinker, the core component of cement.
After cooling, the clinker is ground with gypsum and other additives to produce the final product. The process concludes with packaging or bulk transportation for market distribution. Advanced technologies and automation can significantly enhance efficiency, reduce emissions, and optimize production costs, making them essential for a modern plant.
Establishing a twelve thousand (12,000) MT per day cement plant involves considerable capital expenditure, including costs for land acquisition, machinery, and construction.
A plant of this scale is estimated to require an initial investment of $500 million to $1 billion, depending on location, technology, and infrastructure. Operational expenses include raw material procurement, energy, labor, and maintenance. Cement production is notably energy-intensive, with energy costs accounting for a significant portion of operational expenses. The use of coal, natural gas, or alternative fuels, as well as investments in renewable energy solutions, can help mitigate these costs.
Revenue projections for a plant of this capacity are substantial. With an annual production potential of 4.32 million metric tons and an average market price of $100 per metric ton, annual revenues could exceed $400 million. Under favorable conditions, investors can expect a return on investment within five to seven years. However, success depends on efficient operations, market demand, and the ability to address challenges.
Several obstacles must be navigated to ensure the feasibility of such a project. Energy costs in Nigeria are high, and disruptions in electricity supply can hinder production efficiency. Regulatory compliance, including adherence to environmental standards, often requires additional investment and operational adjustments.
The competitive landscape, dominated by established players such as Dangote Cement, poses challenges for market entry. Furthermore, infrastructural deficiencies, such as poor transportation networks, can impact raw material supply and product distribution. Economic volatility, including fluctuations in exchange rates and inflation, also affects costs, particularly for imported equipment and raw materials.
The global cement market size reached US$ 385.8 Billion in 2023. Looking forward, IMARC Group expects the market to reach US$ 629.9 Billion by 2032, exhibiting a growth rate (CAGR) of five point four percent (5.4%) during 2024-2032.
This growth is fueled by urbanization in emerging economies, increasing investments in infrastructure, and the adoption of eco-friendly cement products. Sustainability initiatives, such as the use of alternative fuels and green technologies, are becoming integral to cement production worldwide. For Nigeria, these global trends present opportunities to align local production with international standards, enhancing competitiveness in both domestic and export markets.
The Nigerian cement market is among the most dynamic in Africa, with significant contributions from established players. Dangote Cement is the dominant producer, with extensive capacity and a vast distribution network. Lafarge Africa and BUA Cement also hold substantial market shares, offering diverse products tailored to different segments. Despite the presence of these industry giants, supply shortages in certain regions highlight opportunities for additional production capacity. New entrants can gain a competitive edge by leveraging advanced technologies, offering competitive pricing, and focusing on underserved markets.
The establishment of a twelve thousand (12,000) MT per day cement plant in Nigeria represents a viable and lucrative investment opportunity. The abundant availability of raw materials, coupled with growing domestic and regional demand, provides a strong foundation for success. By addressing challenges such as high energy costs, regulatory compliance, and market competition, investors can capitalize on Nigeria’s thriving cement market. Moreover, aligning production processes with sustainability trends and incorporating advanced technologies can enhance efficiency and market acceptance.
Cement production plays a pivotal role in Nigeria’s economic and industrial development, serving as a cornerstone for construction and infrastructure projects.
With strategic planning and efficient operations, the proposed plant can contribute significantly to addressing the nation’s housing deficit, supporting government infrastructure initiatives, and driving export revenues. As Nigeria continues to urbanize and modernize, the demand for cement will remain robust, ensuring the long-term viability of investments in this critical sector.
Custom Research Request
Still haven't found what you're looking for?
Speak to our Custom Research Team.
Table of Contents
EXECUTIVE SUMMARY 1.0 Business Overview 1.1 Description of the Business 1.2 Core Values, Vision and Mission Statement 1.3 Value Proposition 1.4 Obtaining a Mining Permit in Nigeria and Associated fees 1.5 Occurrence and Distribution of the minerals in Bauchi state, Nigeria 1.6 Critical Success Factor of the Business 1.7 Current Status of Business 1.8 Description of the Business Industry 1.9 Contribution to Local and National Economy 2. Marketing Plan 2.1 Description of the Product 2.2 Product Packaging and Delivery 2.3 The Opportunity 2.4 Pricing Strategy 2.5 Target Market 2.6 Distribution and Delivery Strategy 2.7 Promotional Strategy 2.8 Competition 3. Production Plan 3.1 Description of the Location 3.2 Raw Materials 3.3 Production Equipment 3.4 Production Process 3.5 Production Cost 3.6 Stock Control Process 3.7 Pre-Operating Activities and Expenses 3.7.1 Operating Activities and Expenses 3.8 Project Implementation Schedule 4.0 Organizational and Management Plan 4.1 Company Profile and Ownership Structure 4.2 Profile of the Promoters 4.3 Management and Governance 4.3.2 Management Support Units 4.4 Details of Salary Schedule 5. Financial Plan 5.1 Financial Assumption 5.2 Start - Up Capital Estimation 5.3 Source of Capital 5.4 Security of Loan 5.5 Loan Repayment Plan 5.6 Profit and Loss Analysis 5.7 Cash Flow Statement 5.8 Viability Analysis 5.9 Net Book Value (NBV) 5.10 Statement of Financial Position 5.11 Investor Returns Analysis 5.12 Investment Consideration 6.0 Business Risk and Mitigation Factors 6.1 Business Risks 6.2 SWOT Analysis
Project Specification:
Additional Info
Get this Report
Direct bank transfer
To order the report, Please do pay the sum of ₦8,500,000 into
Account Name : Foraminifera Market Research Ltd
Account Number : 274 20 569 37
Account Name : Foraminifera Market Research Ltd
Account Number : 101 76 603 95
Account Name : Foraminifera Ventures
Account Number : 011 66 066 32
Make your payment directly into our bank account. Please use your Order ID as the payment reference. Your order will not be shipped until the funds have cleared in our account.
Instructions
After payment call us on 01 -29 52 413 / 08033782777 or email us at foraminiferamarketresearch@yahoo.com with the payment details. After payment confirmation, the soft copy of the report would be sent to you within 24 hours.